If you're a ceramic professional and you're into lapping, there's one thing you take for granted: you only move in single line. One tile follows another, one ribbon, one lane.
Abandoning this principle and optimizing production is the priority of any company in the industry that wants to be even more competitive in the market. Precisely because of this need, the Premier team launched its parallel-row satellite.
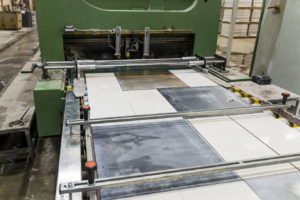
Innovation in lapping
With its particular satellite head, Premier finally proposes an alternative to the "classic" single-file line, which we have called the "four-lane highway."
This is because the Premier satellite allows it to work in multiple parallel rows, like a multi-lane conveyor belt where multiple rows of tiles pass at the same time.
To give you a better understanding of the impact of this revolution, let's take theexample of the kiln: if you are a potter, you know that multiple rows of tiles are fired inside it. A kiln with tiles arranged in a single row would be unthinkable.
To have the same productivity one would have to make a kiln several hundred meters long.
Why not apply the same reasoning to end-of-line processing as well?
Why choose the alternative to Fickert
Currently almost all existing sanding and lapping lines use Fickert heads, which make it impossible to arrange tiles in parallel rows.
The Fickert trowel left and right with a variable tangency line to the tiles, which allows it not to flatten and retain a radiused profile like a tangential tool. In its movement, it can easily hook the side of the tile, lifting it up and damaging the entire tool set, head, tiles, and even the conveyor belt.
Also, when the edge of the tile is slightly curved downward, the parallel juxtaposition of two tiles with the same geometry creates a depression, which cannot be machined by Fickert tools, as they have a minimum tangency line of 100 mm.
In our PREMIER LAB we studied the application of Satellite PREMIER to tiles arranged in parallel rows and found that it is this processing is possible, because:
1. The Satellite PREMIER does not trowel, it rotates on itself and goes from tile to tile by rotating on an inclined axis, pushing the tile against the conveyor belt. In this way we have zeroed the danger of lifting even while keeping the tiles apart.
2. The tangency line is 25 mm divided over two rows of teeth, so the tool is able to penetrate all depressions, even those between juxtaposed tiles
Premier Satellite features
The PREMIER satellite system is capable of developing more kinetic energy than any other system in use and enables higher quality and productivity in end-of-line machining.
The diamond resin tool rotates at a speed of about 1,500 rpm, developing very high kinetic energy, which is equivalent to two Fickert heads.
The composition of the two rotary motions of head and tool, greatly improves the uniformity and speed of removal.
The Satellite Premier is available with a "4-hole" or "Terzago" attachment, grit ranges from 50 to 12,000, and comes in two diameters: 130 or 150 mm.
The adoption of the PREMIER satellite on all processing positions allows lapping of tiles arranged in parallel rows, MULTIPLIFYING line productivity, and greatly reducing costs per m2.
For information and a personalized consultation, contact us now.