After the great success and interest of the webinar on the Tecna-next platform, we decided to propose a complete presentation of the PREMIER satellite system, the latest innovation from the Villaverla company, launched one year ago, it is giving very positive feedback on the market, both in Italy and all over the world, above all in Spain, USA and Latin America.
Applied to the lapping process, the Satellite System is born from the concept that, in order to obtain the maximum yield from the diamond tools, they must work at maximum speed.
In the squaring process, the tools work at speeds over 40 m/s, while today, with the Fickert system, in the lapping process, where the quantity of material removed is much higher, large surfaces and very hard materials are processed, it's reached a maximum speed of only 10 m/s! Therefore it's clear the need to find a system that allows to lap at a higher speed.
After numerous tests at the PREMIER Lab, equipped with a line with 20 spindles for sizes up to 1,200mm, our technicians have developed the new satellite head, which allows to double the lapping speed compared to Fickert tools.
In this way we have obtained a safe, simple, but much cheaper and more efficient system.
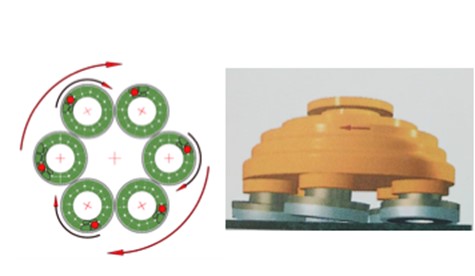
- The satellite system consists in a rotating head on which a series of rotating tools are mounted in a slightly inclined position compared to the advancing plan. The combination of the two concurrent rotary motions of head and tool, greatly improves uniformity and removal capacity. Furthermore, each tool describes in its motion a contact line unique and different from the others present on the same head.
The Satellite, the tool that we mount on these new heads, is composed by a flexible crown, consisting of two rows of blocks distributed on two concentric circles and manufactured by incorporating abrasive and diamond grains in the resin.
The crown is glued to a layer of elastic material, the shock absorber and both are connected to a rigid base that constitutes the body, which is also the attachment to the tool holder of the head.
The tool can be rigid, semi-rigid or elastic depending on the type of elastomer of which the shock absorber is made.
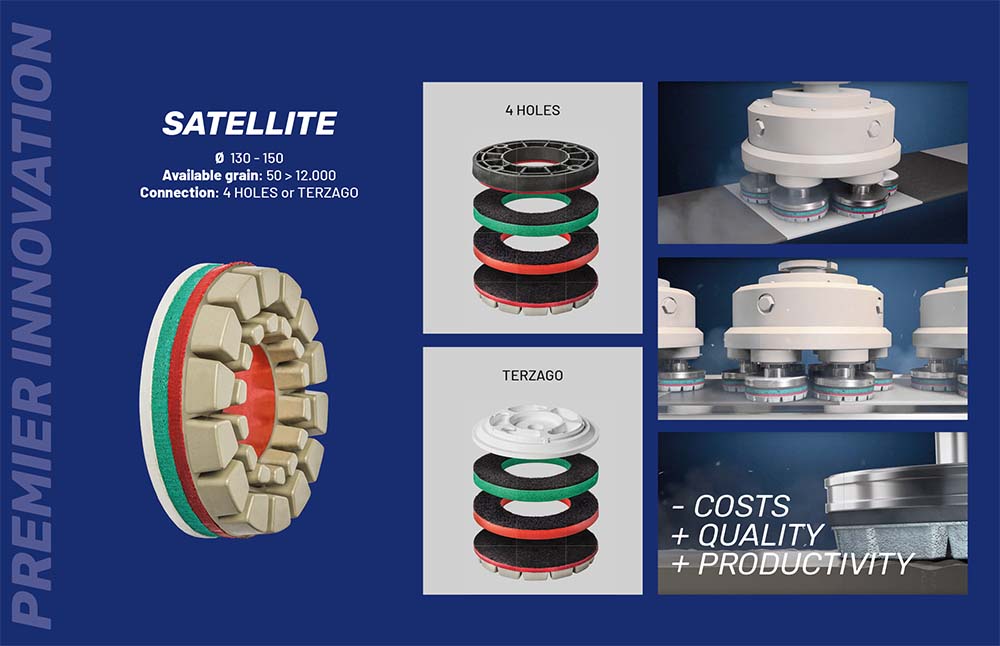
STRENGTHS.
- Superior finish:
- The contact line of the tool is about 25 mm, at least 4 times lower than the Fickert (about 100 mm), this allows the tools to machine any depression.
- Each tool describes in its motion a unique contact line different from the others, avoiding the overlap of the signs and that annoying effect, characteristic of the Fickert, called "progress sign".
- Optimal solution for dark colors, since, with the same removal, it is possible to use tools with a finer grain, obtaining tiles without scratches and with a higher degree of gloss.
- High efficiency: the combination of the rotary motion of the head and that of the tool allow the system to develop a much higher cutting speed, with a high increase in productivity compared to the Fickert.
- Reduction of costs per m2: the best use of the abrasive increases the life of the tool, reducing costs.
- Reduction of maintenance costs: the pressures applied to the heads are much lower, this reduces the wear of the mechanical parts.
- Ease of use and handling: the attachment points in a backward position and the satellite slightly inclined compared to the advancement plan, facilitate the tiles entrance and allow it to overcome differences in height of several millimeters without damaging the material or the tool.
- High versatility: the resin and diamond tool is modular, can be used with or without shock absorber, this allows you to change the set-up according to the degree of planarity desired.
- Eco-sustainability: the satellite has a much longer life than the Fickert tool (3 times for coarse-grained tools and 2 times for fine-grained ones), therefore, the complete system allows to reduce the quantity of waste produced annually by end-of-line machines.
FUTURE EVOLUTIONS:
LAPPING IN PARALLEL ROWS
Using the slight inclination of the tools compared to the advancement plane, which makes it easy to overcome any steps between two consecutive tiles, PREMIER technicians have successfully experimented the lapping process in parallel rows, which allows you to multiply the productivity of a line.
This is absolutely impossible with the Fickert, which trowel left and right and can easily hook the side of the tile, lifting it up and damaging the entire tool set, head, tiles and even the conveyor belt.
Video: lapping in parallel rows
POLISH AND POLISHING-LAPPATO WITH THE SAME LINE
PREMIER has successfully studied the applicability of metal satellites on an existing only polishing-lappato line, transforming it, with only tools replacement, into a line capable of polishing technical porcelain stoneware tiles and lapping glazed tiles.
By applying the satellite heads to a lapping line, the first "Levi-lapping" machine was born, capable of calibrating / polishing and lapping, avoiding the use of bulky and old sizing machines.